zınc concentrate
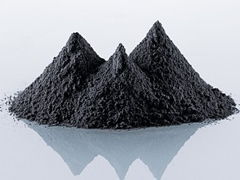
Facts
Origin
- Australia
- Canada
- China
- India
- Peru
- USA
Stowage Factor (in m3/t)
1,11 m3/t (zinc ashes)
Humidity / Moisture
–
Oil Content
–
Ventilation
–
Descrıptıon
Zinc, in commerce also spelter, is a metallic chemical element; it has the symbol Zn and atomic number 30. It is the first element of group 12 of the periodic table. Zinc is, in some respects, chemically similar to magnesium, because its ion is of similar size and its only common oxidation state is +2. Zinc is the 24th most abundant element in the Earth’s crust and has five stable isotopes. The most common zinc ore is sphalerite (zinc blende), a zinc sulfide mineral. Zinc production includes froth flotation of the ore, roasting, and final extraction using electricity (electrowinning).
Zinc, also referred to in nonscientific contexts as spelter, is a bluish-white, lustrous, diamagnetic metal, though most common commercial grades of the metal have a dull finish. It is somewhat less dense than iron and has a hexagonal crystal structure.
The metal is hard and brittle at most temperatures but becomes malleable between 100 and 150 °C. Above 210 °C, the metal becomes brittle again and can be pulverized by beating. Zinc is a fair conductor of electricity. For a metal, zinc has relatively low melting (419.5 °C) and boiling points (907 °C). Its melting point is the lowest of all the transition metals aside from mercury and cadmium.
Many alloys contain zinc, including brass, an alloy of copper and zinc. Other metals long known to form binary alloys with zinc are aluminium, antimony, bismuth, gold, iron, lead, mercury, silver, tin, magnesium, cobalt, nickel, tellurium and sodium. While neither zinc nor zirconium are ferromagnetic, their alloy ZrZn2 exhibits ferromagnetism below 35 K.
Grade: Special high-grade (99,990%), high-grade (99,95%), intermediate (99,5%), brass special (99%), prime western (98%).
Forms available: Slab, soled (strip, sheet, rod, tubing), wire, mossy zinc, zinc dust powder (99% pure), single crystals, zinc anodes.
Applıcatıons
Use: Alloys (brass, bronze, and die-casting alloys), galvanizing iron and other metals, electroplating, metal spraying, auto parts, electrical fuses, storage and dry cell batteries, fungicides, nutrition (essential growth element). Roofing, gutters, engravers’ plates, cable wrappings, organ pipes.
Zinc is a material that has gone through substantial changes in the way that it is used and in the way that it is perceived, both by specialists and by the general public. The broad categories of end use remain much the same, i.e. coatings to protect iron and steel, brass, zinc alloy castings, sheet for building applications and a range of chemical applications. However, within these broad areas there are major differences in process and product which have given a new lease of life to what could otherwise have become a rather boring traditional material.
Zinc Coatings on Steel
One of the biggest uses of zinc is in making protective coatings for steel. The development of the wide range of zinc coatings arose from two happy accidents of chemistry, the relatively slow and predictable rate of atmospheric corrosion of zinc compared with steel, and the relative positions of zinc and iron in the electrochemical series. Zinc will corrode preferentially to give cathodic protection to iron when both are in contact in an aqueous medium. This is used to good effect to protect immersed structures such as ships’ hulls, drilling rigs and pipelines. It also means that any bare areas in a zinc coating on steel, caused by damage or operations such as cutting or drilling, are still protected by the surrounding zinc.
Shıpment / Storage / Rısk Factors
Zinc and zinc products
May have dangerous and hazardous properties. When dealing with these commodities it is advisable to make reference to the ‘International Maritime Dangerous Goods Code’. Zinc and some manufactures or derivatives thereof are variously affected by water, salt or fresh, depending on the nature of the commodity and its uses; the monetary loss will reflect the cost of the remedial treatment and/or variation of quality, etc., of the ultimate product or by-product.
Zinc (Slab)
– Zinc in massive form is liable to superficial corrosion by immersion in or exposure to salt or fresh water. While the corrosion product can be fairly easily removed by brushing, its presence leads to an increased loss in subsequent melting operations and may therefore represent some loss in value.
Zinc Ashes
– Class 4.3 Dangerous when wet.
Liable to give off dangerous gases in contact with water or very humid atmosphere accompanied by heating. Should be packed in effectively closed tin cans or steel drums.
Zinc Chloride – IMDG Class 8 Corrosive
Solution or solid, corrosive, burns the skin.
Zinc Concentrates – When shipped in bulk may be subject to loss in weight and liquefaction; see also Concentrate (of Minerals). The presence of chlorides reduces the value of the concentrates and contact with sea water results in the deterioration of value due to the increase of chlorine content. The extent of the chlorine content determines the degree of damage. At the time of shipment the concentrates may contain a small percentage of moisture, and if it is proposed to overstow with other cargo, it is recommended that the ore be double dunnaged and double ‘sisal’ paper be used to prevent the rising of moisture damaging cargo stowed on top.
Zinc Dust – IMDG Class 4.2 Spontaneously combustible, also dangerous when wet – A hazardous cargo which should be shipped in hermetically sealed lined cases or metal drums. Evolves hydrogen when in contact with water, humid atmosphere, etc., and may ignite. Exposure to moisture should be avoided. Would require complete reprocessing if wet.
Zinc Phosphide – IMDG Class 4.3 Dangerous when wet – Insoluble in water and in the absence of air will decompose only at a very high temperature. It is unlikely, therefore, that this commodity will suffer damage by heat unless this is higher than the melting point of zinc. Reacts violently with oxidizing agents, produces toxic and flammable phosphine by reaction with acids. Toxic by ingestion and a deadly poison.
Zinc Sheets – Access of water between closely packed sheets by condensation or otherwise may damage them through the formation of a white corrosion product known as ‘white rust’. This will reduce coating thickness and spoil the appearance of both galvanized and zinc sheets. These effects are largely due to access of moisture in a limited supply of air and should be avoided by spacing the sheets, or storing or stowing in a dry well-ventilated place. Any sheets that have become wet during transit should be wiped dry before storage. Where outside wrappers are clean and dry, with no signs of water entry, but the sheets themselves show a white deposit, it is possible that the sheets have been packed in a warm and moist atmosphere with subsequent cooling of the sheets causing condensation, giving rise to corrosion.
Note: Consult the IMSBC Code (International Maritime Solid Bulk Cargoes Code) on zinc ashes/concentrates, and IMDG Code (International Dangerous Goods Code) on zinc products for overseas transport.
Editor Note
Above cargo information received from www.CargoHandbook.com with their permission. If you need further information for cargoes pls visit www.CargoHandbook.com.