Sulphur
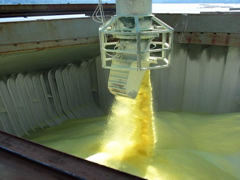
Facts
Origin
–
Stowage Factor (in m3/t)
- 0,74 to 1,11 m3/t (formed, solid)
- 0,85 to 0,95 m3/t (crushed lump and coarse grained)
Humidity / Moisture
–
Oil Content
–
Ventilation
See IMSBC Code
Descrıptıon
Sulphur is a chemical element with symbol S and atomic number 16. It is an abundant, multivalent non-metal. Under normal conditions, sulphur atoms form cyclic octatomic molecules with chemical formula S8. Elemental sulphur is a bright yellow crystalline solid when at room temperature. Chemically, sulphur can react as either an oxidant or reducing agent. It oxidizes most metals and several non-metals, including carbon, which leads to its negative charge in most organo-sulphur compounds, but it reduces several strong oxidants, such as oxygen and fluorine.
Sulphur occurs naturally as the pure element (native sulphur) and as sulphide and sulphate minerals. Elemental sulphur crystals are commonly sought after by mineral collectors for their distinct, brightly coloured polyhedron shapes.
Elemental sulphur was once extracted from salt domes where it sometimes occurs in nearly pure form, but this method has been obsolete since the late 20th century. Today, almost all elemental sulphur is produced as a by-product of removing sulphur-containing contaminants from natural gas and petroleum. The element’s commercial uses are primarily in fertilizers, because of the relatively high requirement of plants for it, and in the manufacture of sulphuric acid, a primary industrial chemical. Other well-known uses for the element are in matches, insecticides and fungicides. Many sulphur compounds are odoriferous, and the smell of odorized natural gas, skunk scent, grapefruit, and garlic is due to sulphur compounds. Hydrogen sulphide produced by living organisms imparts the characteristic odour to rotting eggs and other biological processes.
Sulphur is an essential element for all life, and is widely used in biochemical processes.In metabolic reactions, sulphur compounds serve as both fuels (electron donors) and respiratory (oxygen-alternative) materials (electron acceptors). Sulphur in organic form is present in the vitamins biotin and thiamine.
Sulphur is an important part of many enzymes and in antioxidant molecules like glutathione and thioredoxin. Organically bonded sulphur is a component of all proteins, as the amino acids cysteine and methionine. Disulphide bonds are largely responsible for the mechanical strength and insolubility of the protein keratin, found in outer skin, hair, and feathers, and the element contributes to their pungent odour when burned.
Physical properties
Sulphur forms polyatomic molecules with different chemical formulas, with the best-known allotrope being octasulphur, cyclo-S8. Octasulphur is a soft, bright-yellow solid with only a faint odour, similar to that of matches. It melts at 115.21 °C, boils at 444.6 °C and sublimes easily. At 95.2 °C, below its melting temperature, cyclo-octasulphur changes from α-octasulphur to the β-polymorph. The structure of the S8 ring is virtually unchanged by this phase change, which affects the intermolecular interactions. Between its melting and boiling temperatures, octasulphur changes its allotrope again, turning from β-octasulphur to γ-sulphur, again accompanied by a lower density but increased viscosity due to the formation of polymers. At even higher temperatures, however, the viscosity decreases as depolymerization occurs. Molten sulphur assumes a dark red colour above 200 °C. The density of sulphur is about 2 g•cm−3, depending on the allotrope; all of its stable allotropes are excellent electrical insulators.
Chemical properties
Sulphur burns with a blue flame concomitant with formation of sulphur dioxide, notable for its peculiar suffocating odour. Sulphur is insoluble in water but soluble in carbon disulphide and, to a lesser extent, in other nonpolar organic solvents, such as benzene and toluene.
Use: sulphuric acid manufacture, pulp and paper manufacture, carbon disulphide, rubber vulcanization, detergents, petroleum refining, dyes and chemicals, drugs and pharmaceuticals, explosives, insecticides, rodent repellents, soil conditioner, fungicide, coating for controlled-release fertilizers, nucleating agent for photographic film, cement sealant, binder and asphalt extender in road paving (up to 40%), base material for low-temperature mortars.
Shıpment / Storage
Yellow, crystalline non-metallic element existing in two stable crystalline state. Both forms are insoluble in water and slightly soluble in common organic solvents. Sulphur is an easily igniting, solid substance and exists in the shape of lumps, bars and as fine-grained to very fine powder. Yellow in colour, contact of sulphur with chlorates, nitrates, perchlorates and permanganates leads to the risk of explosion. Sulphur is not soluble in water and when in contact with oil and fat there is the danger of fire. The sulphurous smell can affect piece goods, potatoes and other consumption articles.
Sulphurs dust, sulphur in water and burned sulphur can be very corrosive. Silver in the vicinity of sulphur turns black and paint may scale off. A cloud of sulphur dust is subject to risk of explosion and will easily be ignited by sparks from e.g. iron to iron, static electricity caused by friction and even among particles of sulphur. The risk of dust explosion can be prevented by proper ventilation of the container during stuffing or unstuffing.
Burning sulphur produces the asphyxiating sulphur dioxide (SO2) and could be extinguished by a layer of cold sulphur or with fresh water. Do not use sea water because the mixture will form a hydrochloric acid.
Measures to be taken prior to stuffing containers
- Container must be very well cleaned and dried before stuffing.
- Ceilings also to be made dust-proof. Dirty sulphur is worthless.
- The floor must be lathed and well stopped.
When stuffing or unstuffing safety equipment must be on hand including breathing apparatus, Draeger gas-tester with tubes (SO2), protective clothing, fresh water and CO2-fire extinguishers. If chutes are being used for loading, they must be electricity connected with the container for discharge of static electricity. During the voyage the temperature in the container may run up to 42°C after departure. This has not to be considered as abnormal and in most cases the temperature will drop again after a while. Resuming: 1. Dunnage removed from the area. 2. Containers thoroughly cleaned and dry. No loose steel parts to be left behind. 3. Floors made sulphur-proof. 4. In case of fire, if justified, use as little water as possible and do not use salt water. Preferably CO2-extinguishers. 5. Well ventilated. 6. Breathing apparatus, Draeger gas tester with kept tubes, protective clothing, CO2-extinguishers and fresh water ready for immediate use, when stuffing/unstuffing.
Additional information on sulphur
Sulphur is insoluble in water but highly flammable. Sulphur will readily ignite in contact with flame, or spark. Metal chains or slings should not be used to load sulphur, thus avoiding the possibility of ignition by spark. Should sulphur catch fire it should be smothered with more sulphur or with a very fine spray of fresh water. The use of sea water should be avoided. A heavy spray or jet may aggravate the fire. In the manufacture of sulphuric acid it is essential that the sulphur used is free from sodium chloride, otherwise hydrochloric acid gas is likely to be formed during processing, with serious consequences to plant. It is, however, a comparatively simple matter to wash sea damaged sulphur and so remove the sodium chloride. As sulphur is not soluble in water, the sodium chloride may sometimes be removed by leaving the crude sulphur in the open for some time exposed to rain. Salt water damage to sulphur which is intended for use in the paper industry renders it unfit for that purpose. Sea water will turn sulphur black. Sulphur is corrosive to iron and steel, and holds should be lime-washed before loading.
Sulphur cargoes – a reminder on good practice on board bulk carriers
Major problems on board a bulk carrier have again highlighted problems encountered when carrying bulk sulphur cargoes. Relatively minor lapses or omissions in a vessel’s preparation to carry cargo can lead to major insurance claims. The following points and procedures are among those that must be followed if cargo claims and/or hull and machinery claims are to be avoided:
- all residues from previous cargoes must be removed.
- all loose paint, rust and/or scale must be removed.
- all traces of chlorides must be removed, especially those remaining after washing cargo holds with seawater.
- Cargo holds must be thoroughly fresh water washed and bilges drained.
- The cargo holds should be ‘grain clear’ prior to loading (i.e. equivalent cleanliness requirements as for grain cargoes).
- Holds must be inspected and approved and hatches must be watertight.
- See below for additional advice
Materials which present corrosive hazard of such intensity as to affect either human tissue or the ship’s structure should only be loaded after adequate precautions and protective measures have been taken. Such preventative measures include placing a barrier between cargo and hull steelworks, this is commonly lime wash. If lime wash is to be used it should be of a strength typically 60 kg of lime to 200 litres of fresh water. Recommended thickness will be notified by attending surveyors. Crews should always follow shipper’s instructions. Holds must be carefully cleaned on completion of carriage and safe discharge of sulphur cargoes. Carriers should exercise extreme caution when carrying sulphur cargoes and be fully aware of the potential problems prior to fixing the vessel and loading the cargo. Personnel employed on board vessels carrying sulphur cargoes should wear correct personal protective equipment as necessary. Sea staff must be made aware of any potential safety risks or hazard to health.
The below report was produced by the Carefully to Carry Committee – the UK P&I Club’s advisory committee on cargo matters.
Sulphur is a relatively cheap commodity, which is used in the manufacture of fertilizer. It is not only a byproduct of the petrochemical industry, but also found in its natural form. After processing, it is often shipped in prilled form. Substantial quantities of sulphur are produced in the Alberta province of Canada, most of which is shipped from Vancouver. It is shipped from other ports, including San Francisco, Long Beach, Aqaba and Jubail. Sulphur shipped from Vancouver is generally described as ‘Canadian bright yellow formed sulphur’. The sulphur suppliers warrant strict purity specifications to their customers and so are concerned at the risk of contamination.
Dry sulphur does not react with bare steel, but wet sulphur (sulphur containing free water) is potentially highly corrosive. Cargoes of sulphur in bulk are normally afforded exposed storage and are thus subject to inclement weather and consequent moisture content. The stock will also include a percentage of sulphur dust particles. In order to prevent contaminated air emissions, it is the practice, especially in Canada and the USA, where loading wharves are situated in built-up areas and the dust is considered to be a pollutant, for the environmental authorities to insist upon the use of a water spray during handling to keep down the dust. This practice, now widely adopted in other loading ports, may lead to difficulties during and after the period of ocean transportation. Despite the fact that very large quantities of sulphur are carried annually by sea, the vast majority are carried without significant damage to the carrying vessels.
Corrosion
When sulphur is loaded, any retained free water filters to the bottom of the holds during the voyage. From there it is pumped out via the bilges. Some water remains on the tank tops, and together with the fines, produces a sulphurous mud. A great deal of research has been undertaken to understand and mitigate corrosion to vessels’ structures during the handling and transportation of sulphur. There are two processes whereby a corrosion reaction can occur, namely acidic and electrochemical corrosion.
Acidic corrosion
This involves a reaction between an acid and elemental iron (steel). The acid involved is sulphuric acid (H2SO4). Corrosion does not become significant until the acidity of the solution increases to or below pH2.
Electrochemical corrosion
It has been established that the electrochemical reaction involves a redox (reduction/oxidation) reaction between iron and sulphur. The specific requirements for this reaction to take place are that sulphur and iron are in direct contact and that the sulphur must be wet.
Much of what is known about the electrochemical process is based upon research carried out in the 1980-90s at the University of Calgary by Professor JB Hyne and Dr Dowling. This work has established the characteristics of the reaction as follows:
- The reaction has a maximum rate at around neutral pH.
- The reaction displays auto-catalytic behaviour under anaerobic conditions (existing without the presence of oxygen) – the reaction product promotes further reaction to occur.
- The reaction proceeds to a greater extent and at a higher rate under anaerobic rather than aerobic conditions. The initial by-product of the corrosion process is ferrous sulphide (FeS), otherwise known as Makinawite – a black/brown substance, spontaneously combustible upon contact with oxygen.
- The reaction displays typical temperature dependence – the rate approximately doubles for every 10°C rise in temperature.
Experience has shown that it is electrochemical rather than acidic corrosion that is responsible for the largest proportion of damage occurring to a ship’s hold structures on passage.
The following prudent measures, to preclude risk of damage as a result of loading sulphur, should be adopted:
- Make good all damages to paint coatings on hopper tank plating, bulkheads, bulkhead stools, internal ship’s side plating frames and internals to the height to which the cargo will be in intimate contact, and loose rust and scale removed from the underside of hatchcovers.
- Aluminium or epoxy resin based paints appear to be most effective.
- Whereas the current rules of Classification Societies do not require tank top plating to be coated, it is important and accepted that paint coatings serve to provide protection to the plates during the carriage of sulphur.
- Lime wash as per owner’s/shipper’s/charterer’s instructions and to the satisfaction of the pre-load surveyor.
- Cover the bilge strainer plates with hessian.
- Prior to loading the master should issue a formal letter addressed to the stevedoring company and to the shippers requiring great care in the handling of the cargo to prevent the grabs from loading from heights of 1.0 m from the tank top or cargo level in order to avoid the generation of powder.
- Prior to loading the master should obtain a DCD (Dangerous Cargo Declaration) from the shippers or their agent
- During the loaded voyage, maintain bilge levels below tank top level. Keep a careful bilge pumping record, which should also include estimates of the volumes of water ejected from the holds.
- Remove all residues of sulphur from the holds upon completion of discharge and thoroughly wash down the holds with sea water and finally fresh water.
- Should corrosion have occurred, it must be removed by chipping or shot blasting before washing. The bare steel touched up with paint coatings.
The presence of chlorides – in the form of salts, such as sodium and potassium chlorides – can hasten the interaction between the moist sulphur and ship’s steel. Sodium chloride is for example, a major constituent of both salt cake and dissolved materials found in sea water, while potassium chloride (potash) is regularly shipped from Vancouver. Any trace of these substances will lead to an accelerated corrosion effect, so hold cleanliness prior to loading is of the utmost importance.
To summarise, in order to determine if a vessel is likely to suffer from corrosion damage due to the carriage of wet sulphur and to what degree, the following factors should be taken into account:
- Cargo-related factors and in particular, residual cargo acidity.
- Length and duration of voyage.
- Temperatures encountered during the voyage.
- Effectiveness of lime washing and condition of underlying paint coating
- Proper bilge pumping to remove excess water.
Cleanliness
Prior to loading sulphur, it is recommended that the receiving holds should be in a ‘grain clean’ condition, which requires:
- Removal of all residues of previous cargoes, hard and loose scale from the holds. Access to the upper regions of the holds should be gained by safe equipment. Air wands should be used to dislodge residues of cargo from otherwise inaccessible areas.
- Thoroughly wash out the holds with sea water.
- Thoroughly wash out the holds with fresh water.
The IMO BC Code also states in Section 9.3.1.12:
“After discharge of materials, a close inspection should be made for any residue, which should be removed before the ship is presented for other cargo; such an inspection is particularly important when materials having corrosive properties have been transported.
Lime washing
It should be noted that applying lime wash to cargo hold structures does not totally eliminate, but acts to slow or mitigate the corrosive reaction. Hence ideally, the lime wash is, or should be, applied over existing sound paint coatings. The lime wash acts then in two respects – as an additional physical barrier and also as an alkaline neutralising barrier between the wet sulphur and bare steel / painted surface. The lime wash’s neutralising action will eventually result in it being ‘consumed’ by the sulphur – once this happens, and in the absence of an intact paint coating, the sulphur is once again in direct contact with the ship’s structure and the electrochemical corrosion process can resume.
Experience with Canadian sulphur has shown that the application of a single layer of lime wash can provide good protection to the steel for about 30-40 days, and in some cases even longer. It is recommended that a mixture of approximately 60 kg of lime to 200 litres of fresh water should be used. The lime wash should also be allowed to dry before loading commences, otherwise the protective ‘glaze’ may not form properly.
Gas emissions
Hydrogen sulphide
There are circumstances during the passage and after discharge whereby bulk sulphur can emit small quantities of hydrogen sulphide gas. All areas in which sulphur is stowed or used or which require the presence of personnel should therefore be thoroughly ventilated.
Sulphur dioxide
Masters should also be aware of the possibility that sulphur dioxide may be generated during repairs involving heating/welding in spaces previously exposed to sulphur. Appropriate safety measures should be taken.
Flammability
Masters should be aware that fire might occur when dry sulphur is being loaded as a result of static electricity building up on the loading pipes. These fires can be extinguished by dowsing with sulphur or by the use of a fresh water spray. Ferrous sulphide is pyrophoric (may spontaneously combust on contact with air) and can cause fires near the tank tops during discharge. Such fires maybe be controlled with the judicious use of a fine jet of fresh water.
Rısk Factors
For overseas carriage consult the IMSBC Code (International Maritime Solid Bulk Cargoes Code), IMDG (International Maritime Dangerous Goods Code) and applicable MSDS sheet.
Editor Note
Above cargo information received from www.CargoHandbook.com with their permission. If you need further information for cargoes pls visit www.CargoHandbook.com.